Our Techology
High torque density motor closest to human muscle
"Innovating Human-Robot Coexistence"
Faraday Dynamics Co., Ltd. provides innovative high torque density servo motor solutions to realize 'human-robot coexistence,' the key challenge of the next-generation robotics era.
Our independently developed servo motors achieve world-class torque performance and excellent backdrivability, enabling safe physical interaction between robots and humans.
Frameless Motor
Performance
Comparison Graph

"Torque density (Nm/kg) refers to the continuous torque per unit weight of a motor, and a higher value indicates that the motor is both compact and powerful."
"Continuous torque (Nm) is the torque a motor can sustain; higher values mean greater efficiency and strength."
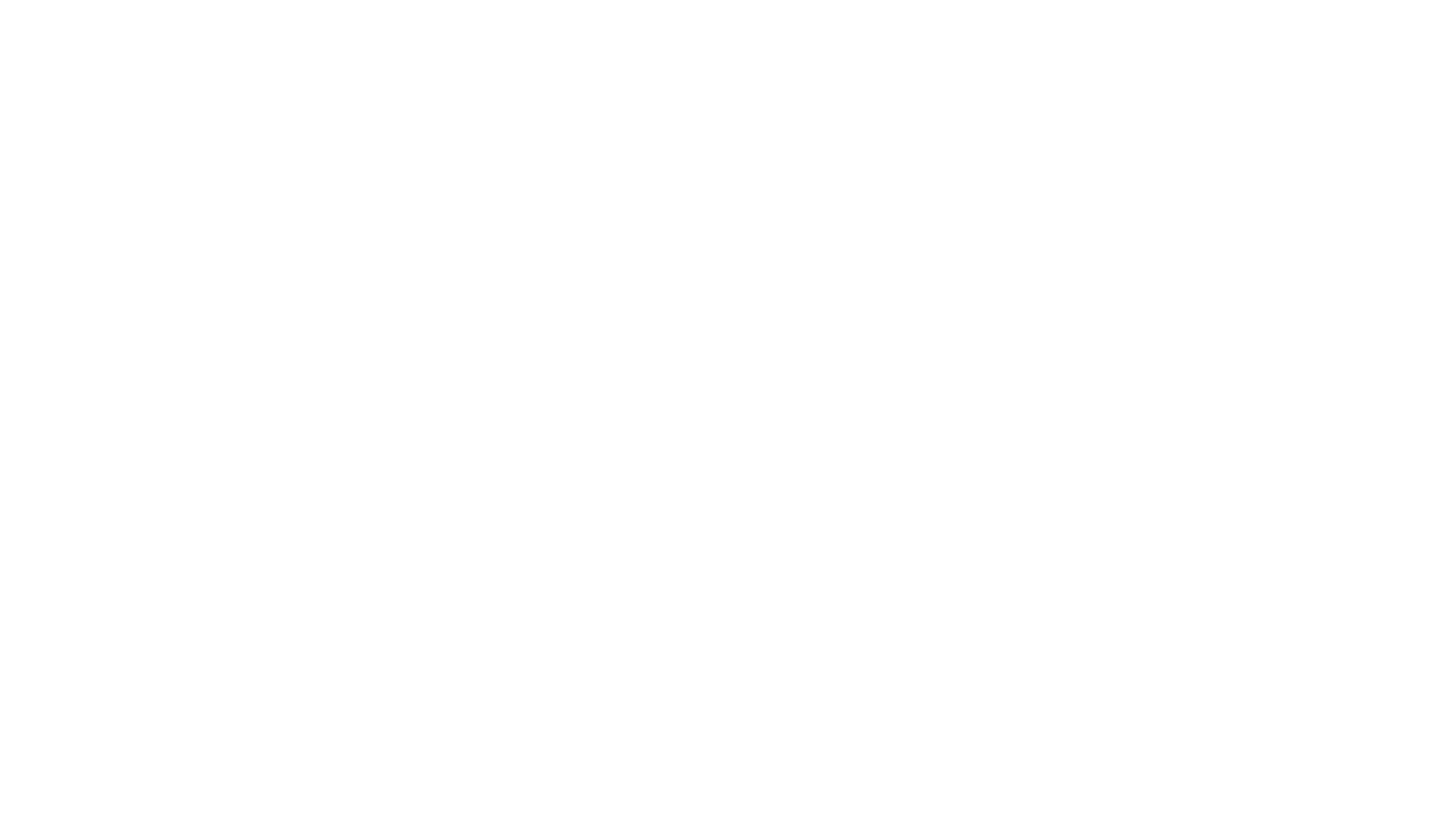
Quasi Direct Drive Motor
Performance
Comparison Graph

"Torque density (Nm/kg) refers to the continuous torque per unit weight of a motor, and a higher value indicates that the motor is both compact and powerful."
"Continuous torque (Nm) is the torque a motor can sustain; higher values mean greater efficiency and strength."
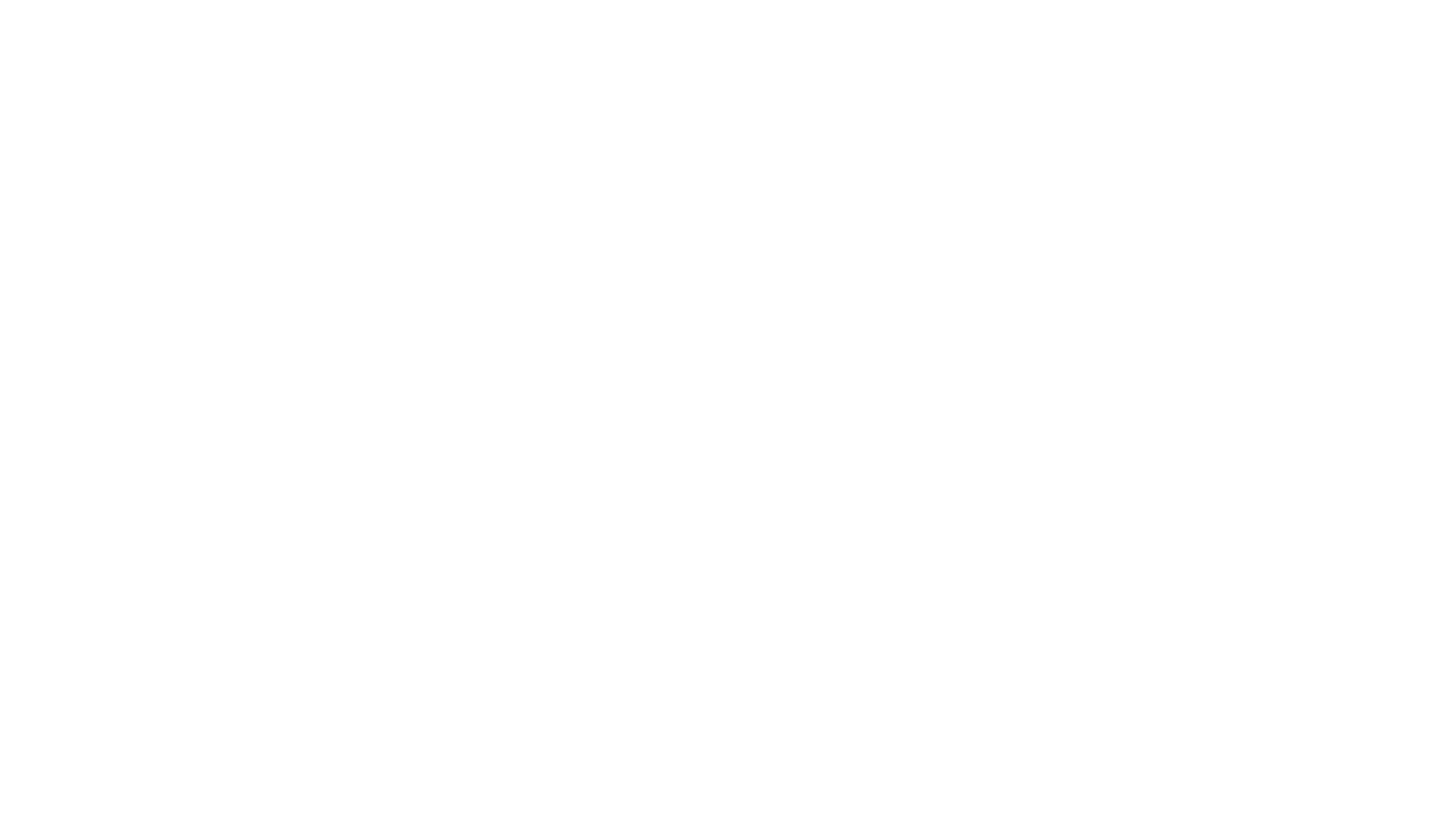

the more the robot's joints can absorb external impacts and perform flexible movements, enhancing safety in human interaction."
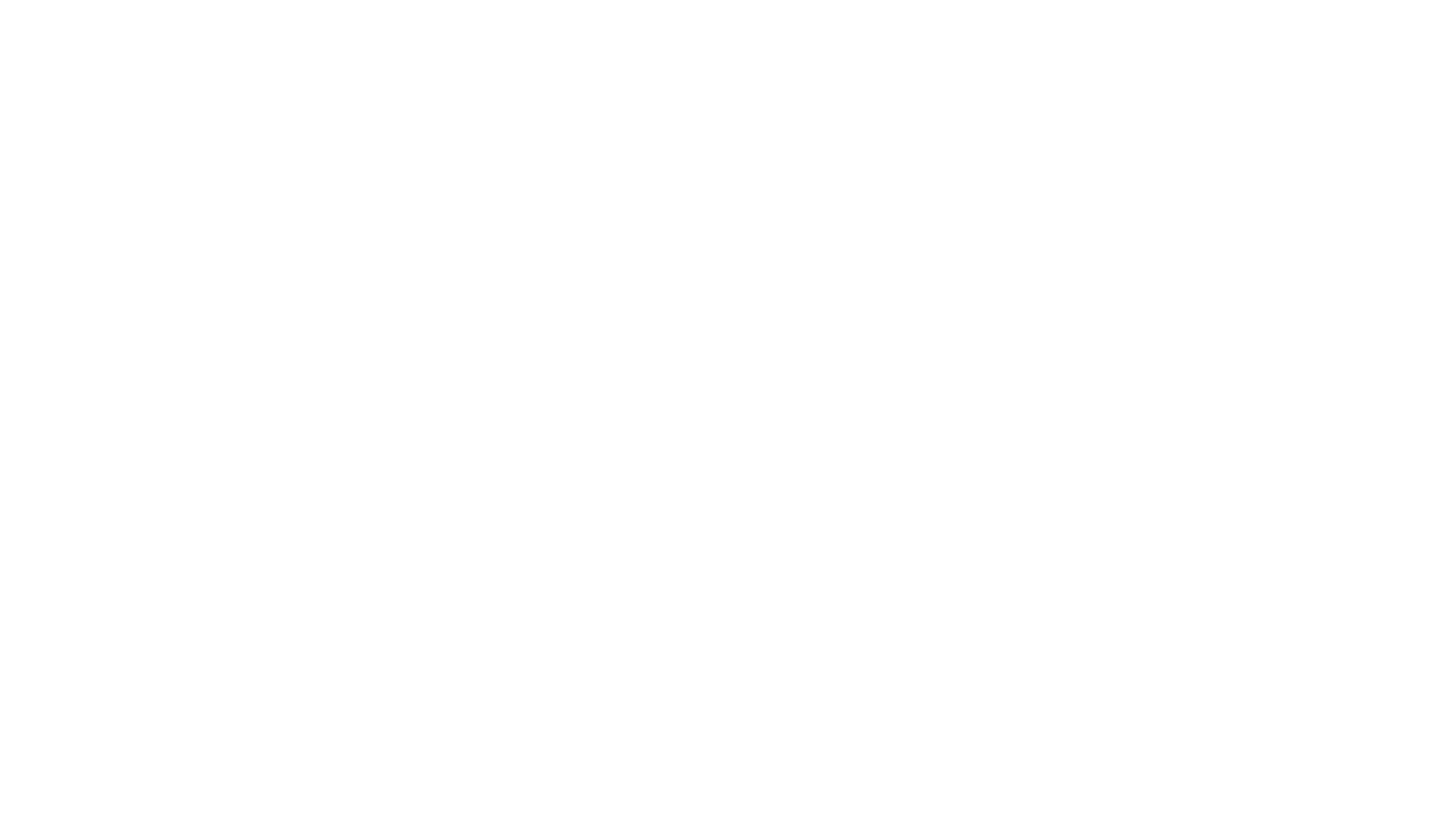
Quasi Direct Drive Motor
Performance
Comparison Graph
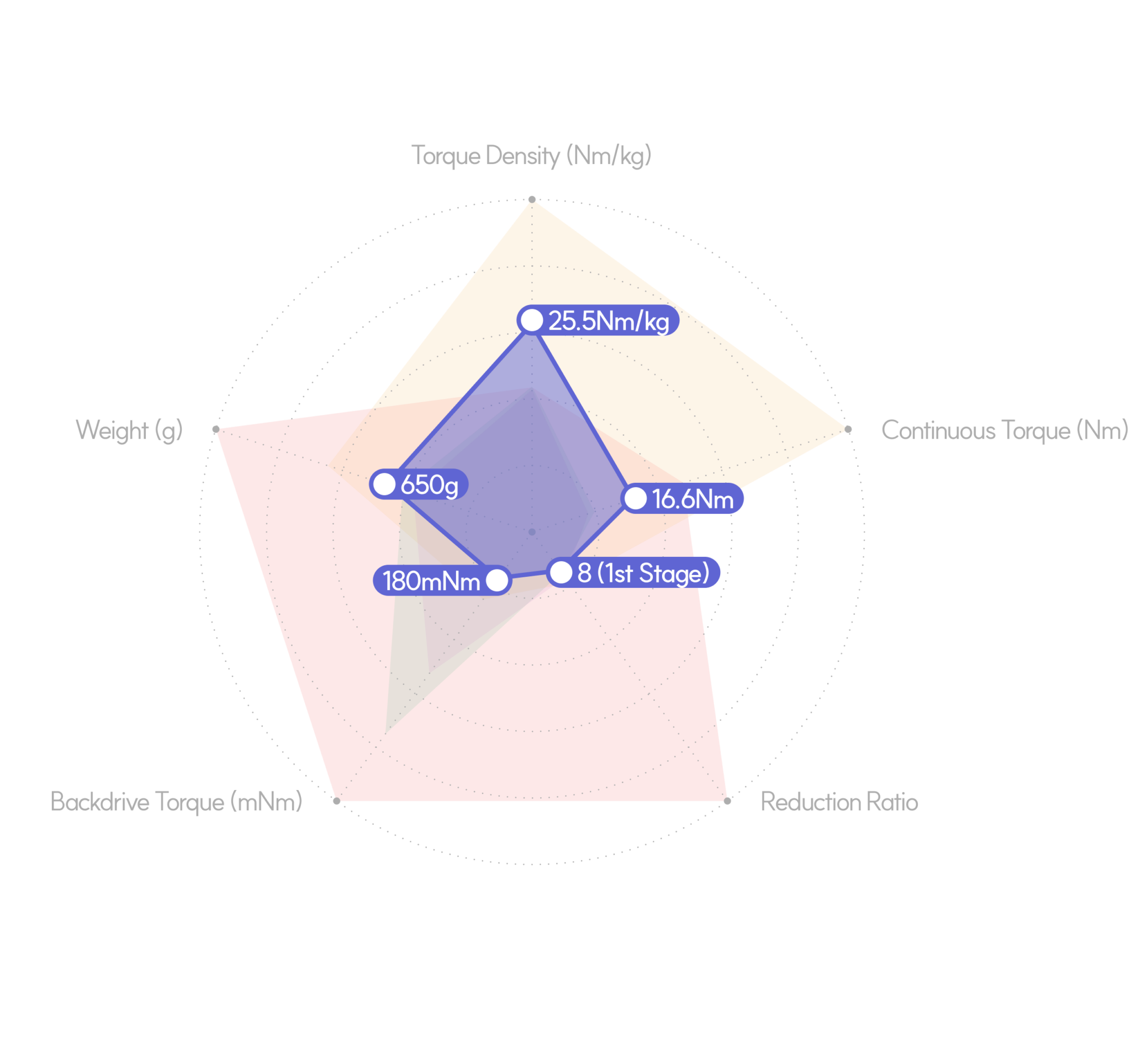
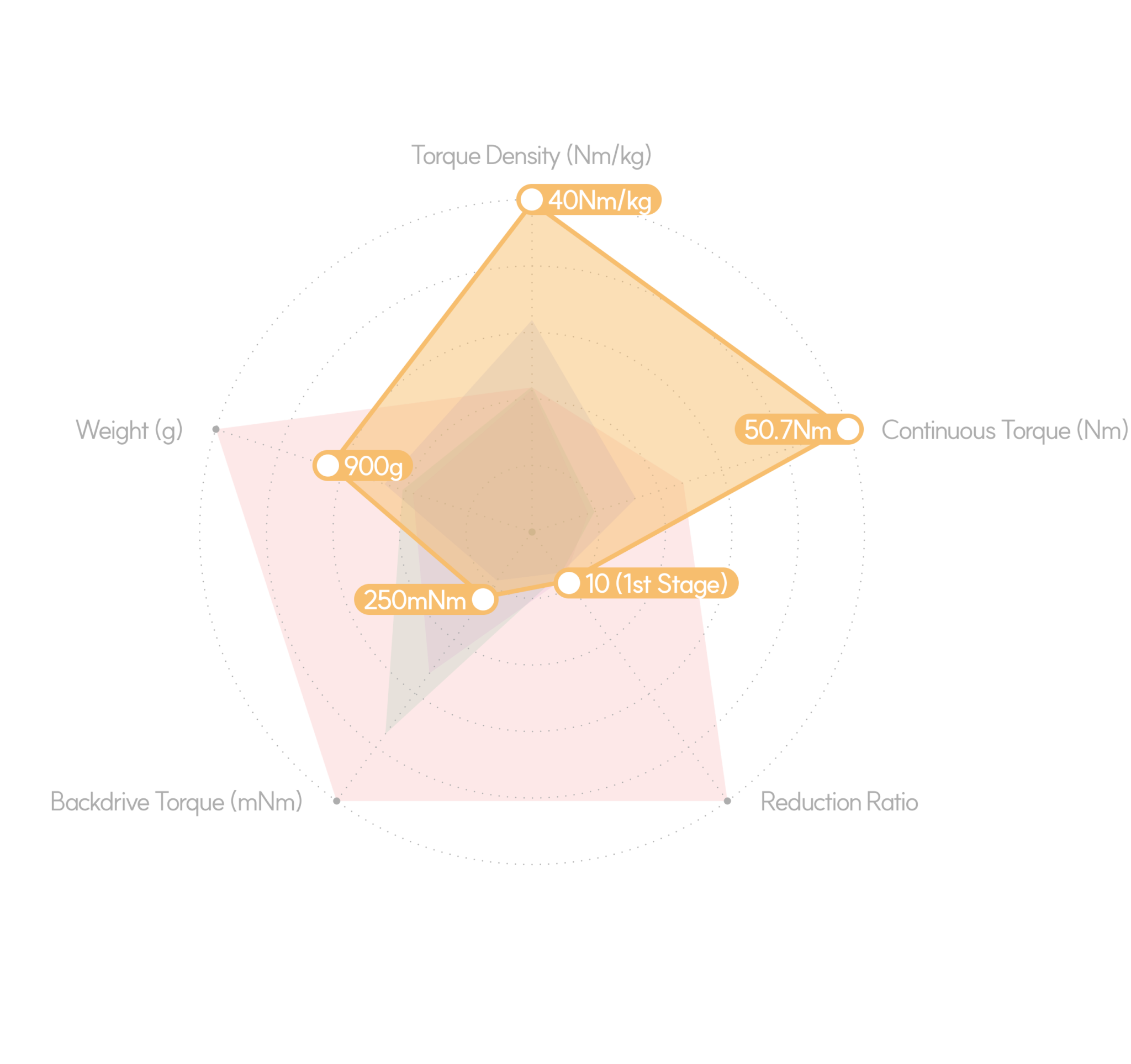
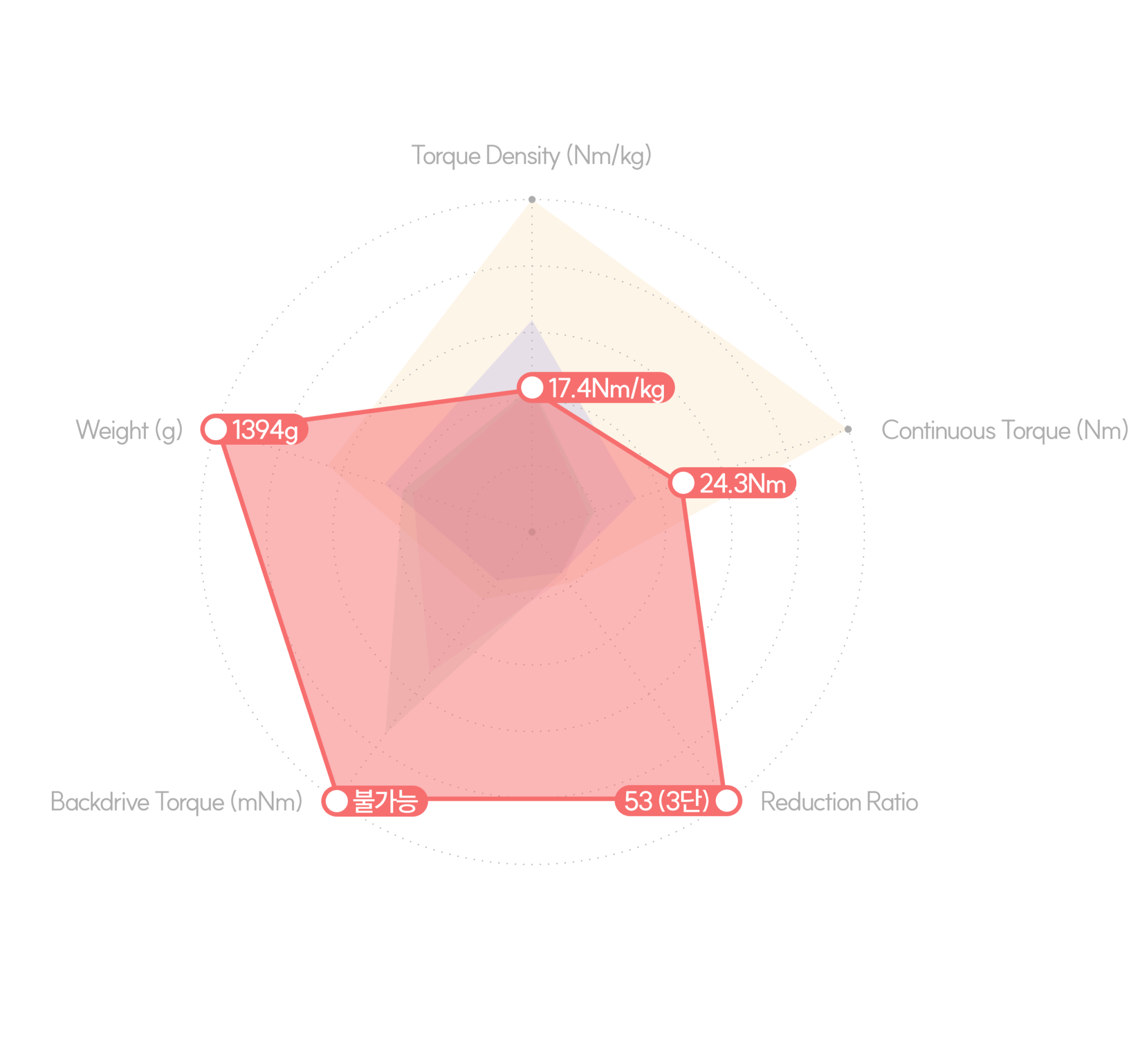
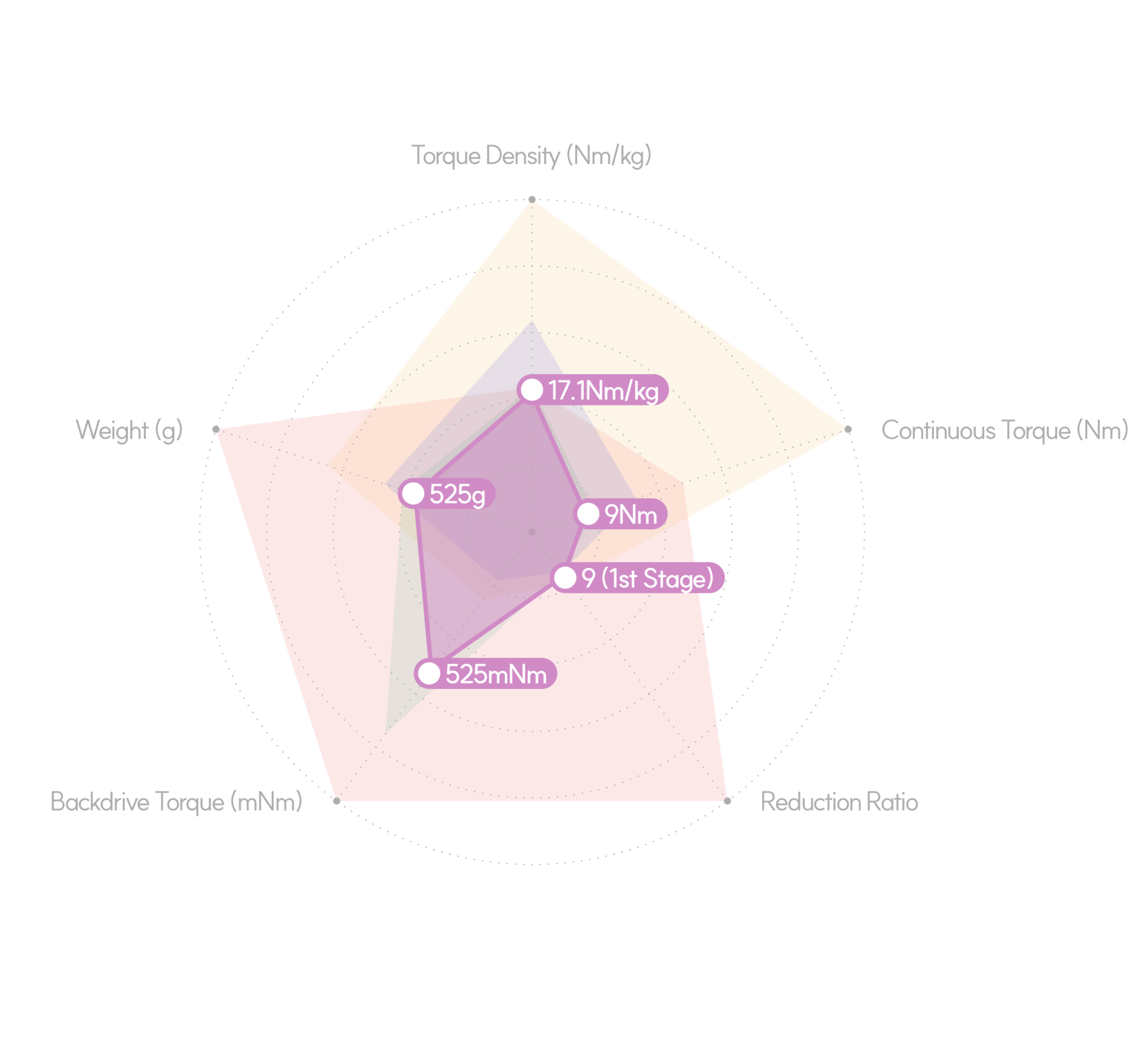
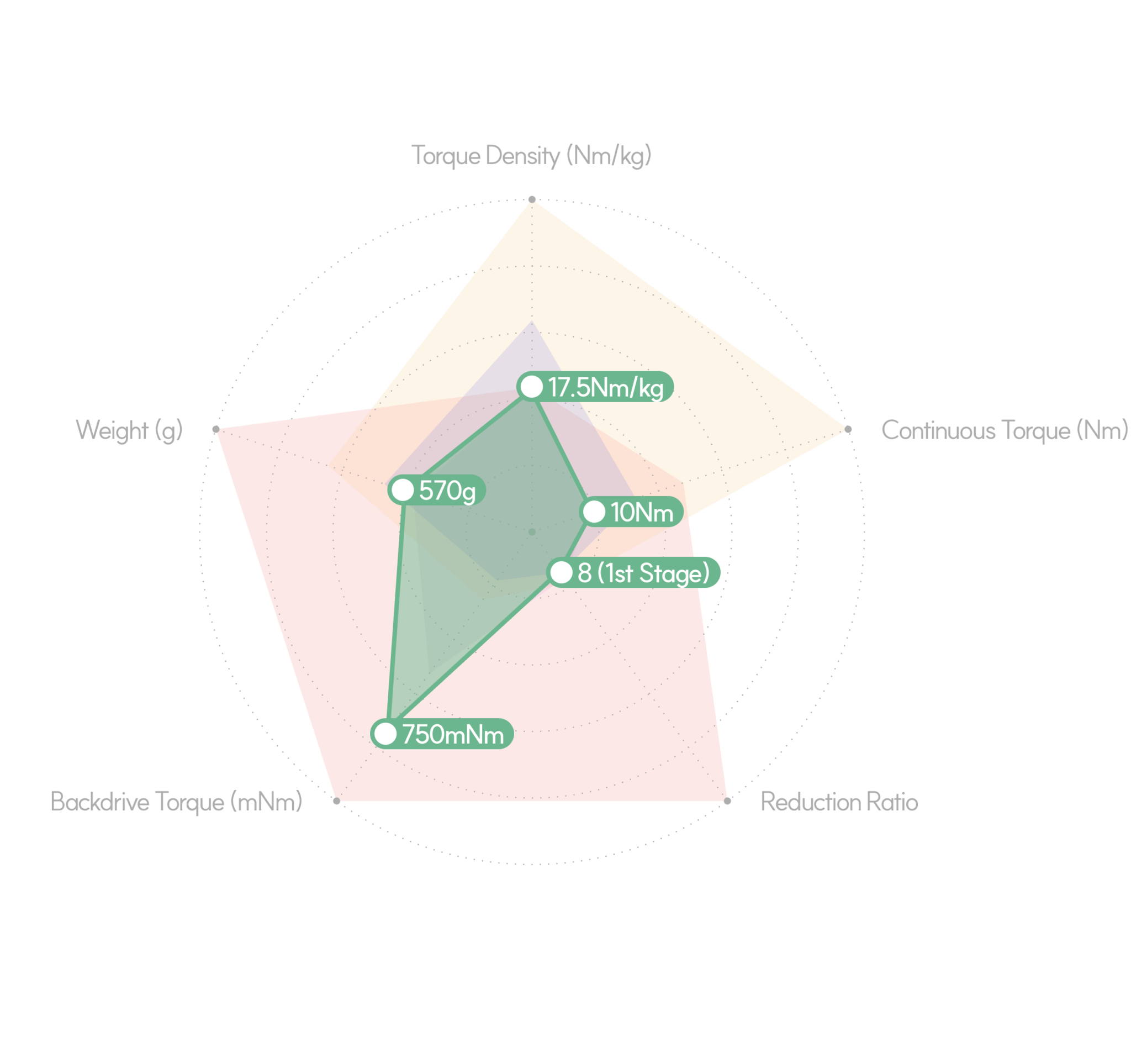
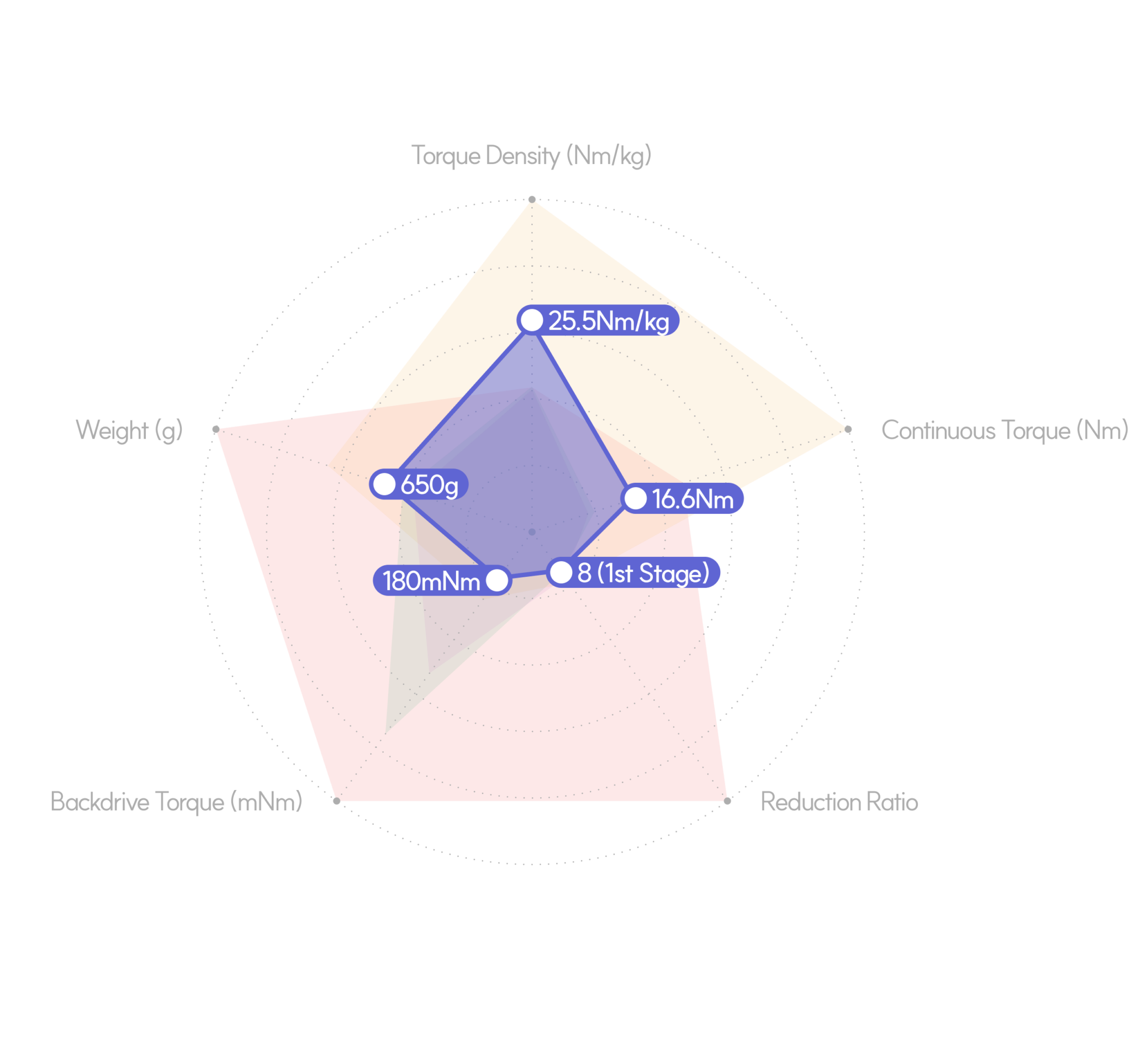
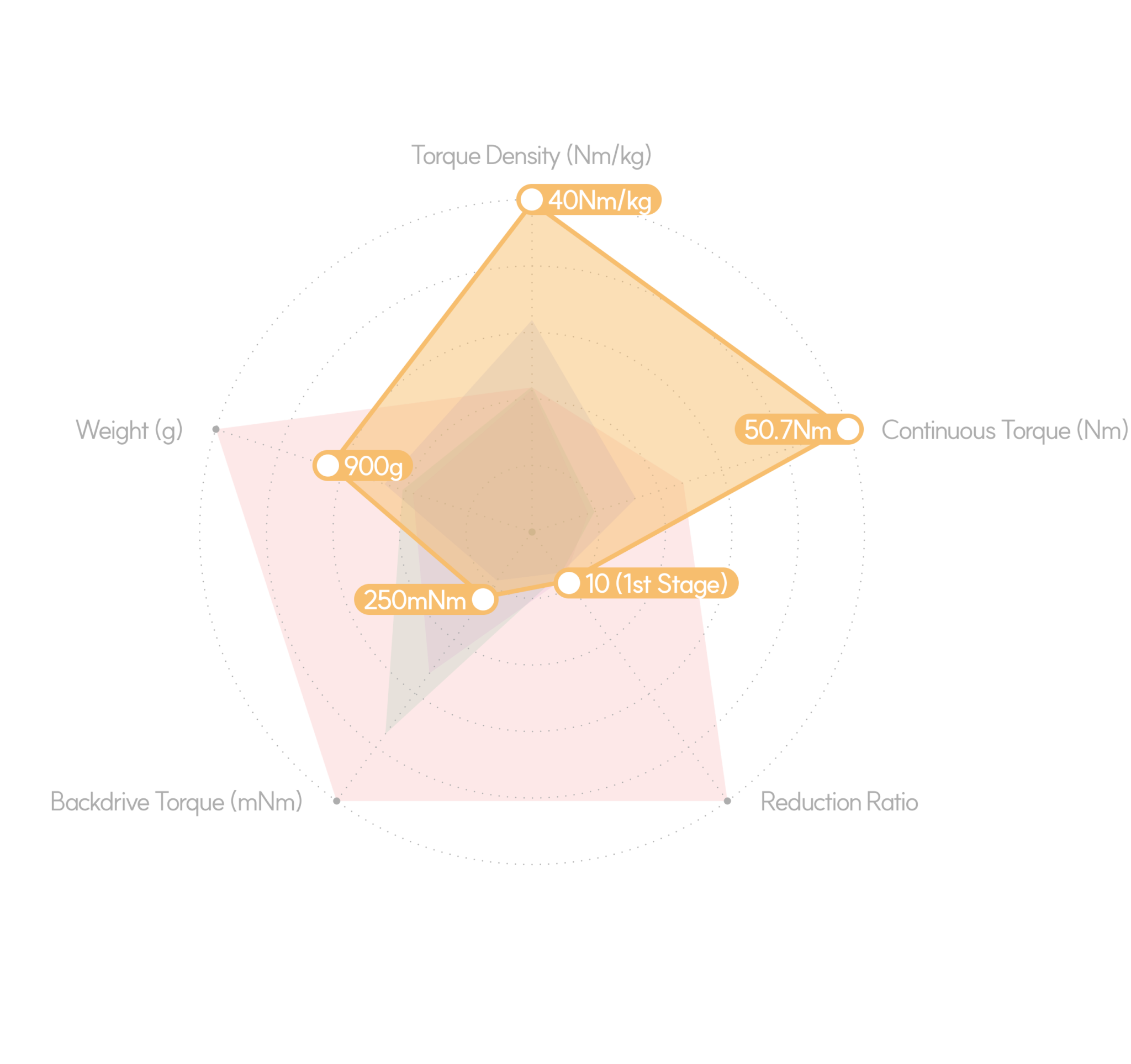
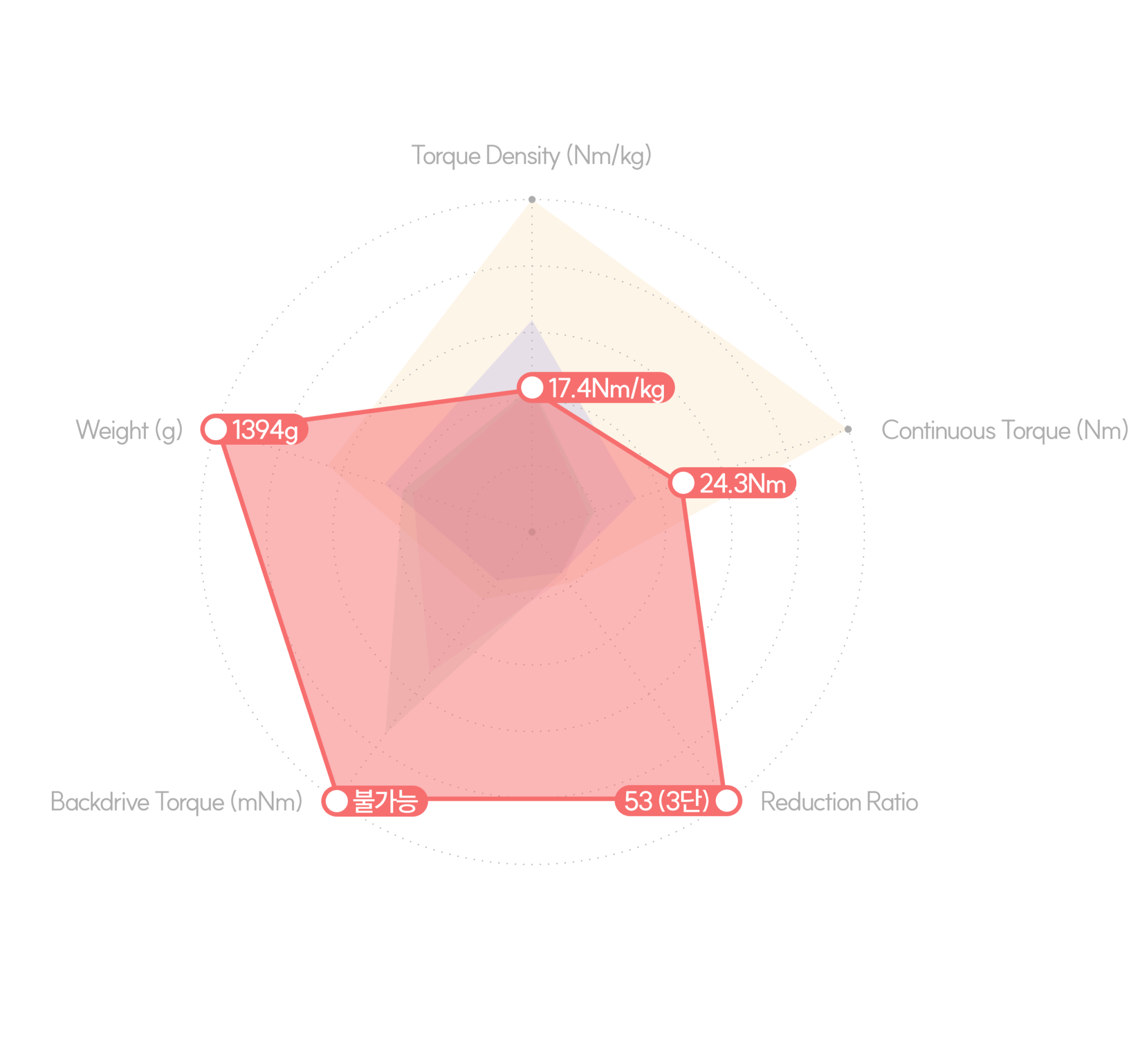
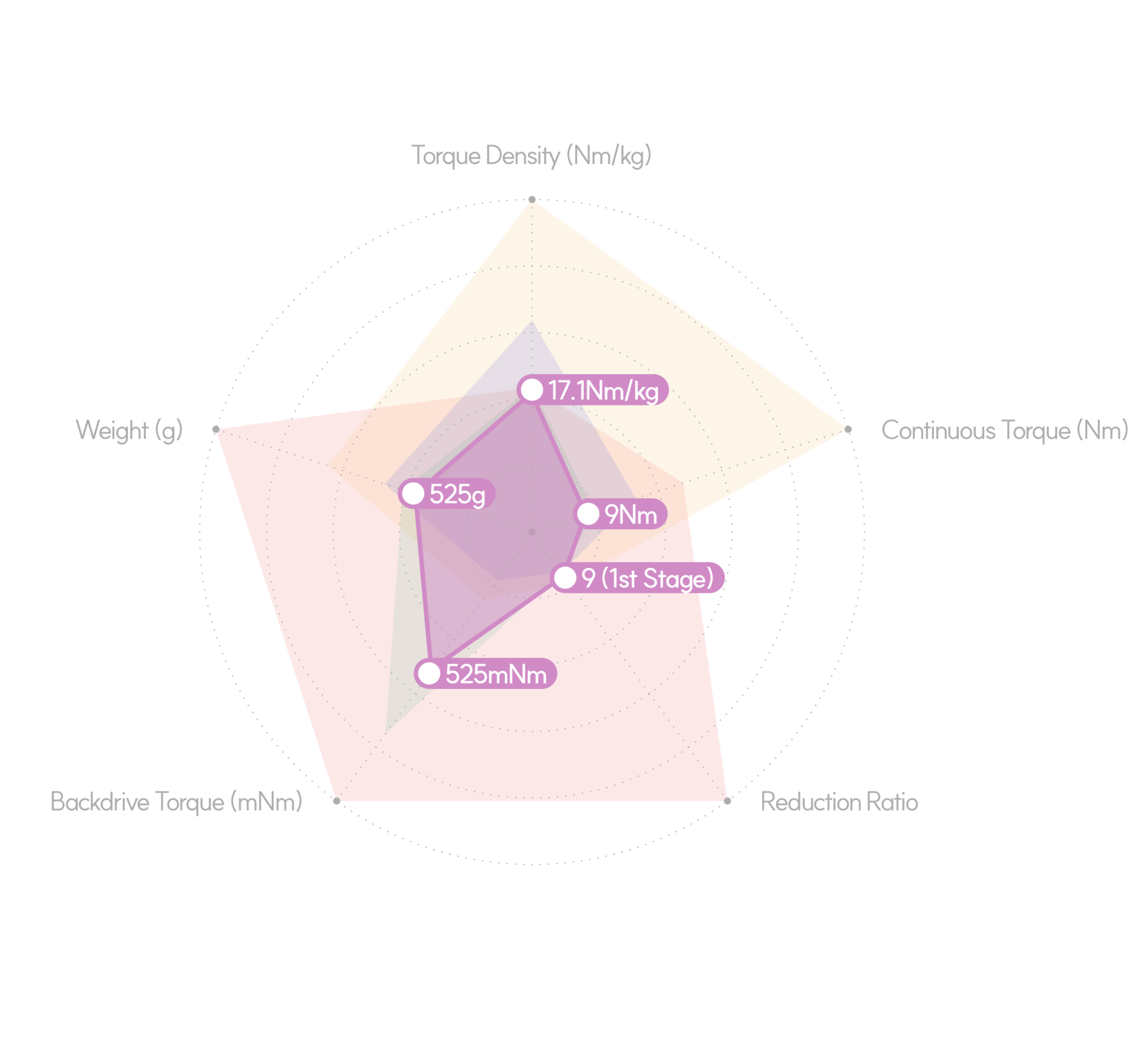
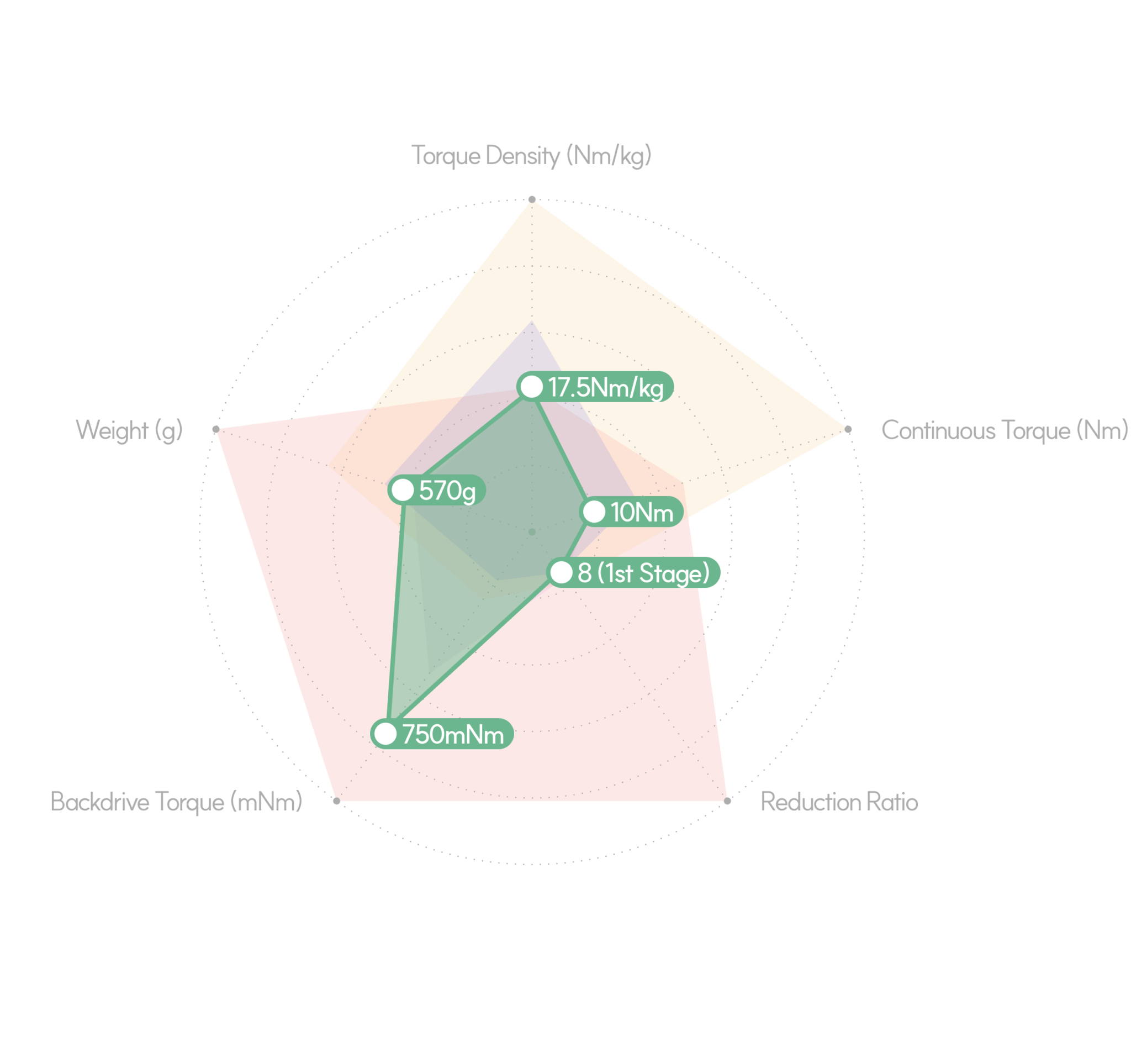
FaradayDynamics™ Technology
Human Muscles and Electromagnetic Induction Law Reborn as High Torque Density Motor Technology
Human muscles exert flexible yet powerful force without reducer friction. Similarly, using high torque density motors minimizes heat generation, prevents thermal damage, and maximizes flexibility. Faraday Dynamics provides optimal performance tailored to customer needs and possesses premium motor technology that will lead the servo motor market.
01
Problems with Conventional Robot Motor Technology
Motors are the most crucial components where robots interact with humans in physical space. However, conventional servo motors for robots necessarily use high-friction reducers due to low torque density, causing excessive stiffness in robot joints. This leads to significant safety concerns, such as causing serious injuries during unexpected collisions with humans. Furthermore, the use of reducers necessitates torque sensors due to nonlinear friction, increasing the production costs of robot applications. The increased weight and size lead to inefficient operation and frequent robot damage. Therefore, future robots such as collaborative robots, humanoid robots, walking robots, wearable robots, and exoskeletons need joints that are both flexible and strong, similar to human joints.
02
Characteristics of Faraday Dynamics Motors
FaradayDynamics’ next-generation servo motors implement characteristics of human muscles. Through new magnetic material development and magnetic field concentration technology, we have achieved world-class torque density and backdrivability. With strong torque output from small current, it demonstrates optimal continuous torque and high efficiency. Additionally, it realizes precise control with less than 2% torque ripple and minimized cogging torque. This innovative technology opens new horizons in future robot development and accelerates the safe introduction of robots into human society.
03
Continuous Research and Development
FaradayDynamics pursues endless innovation beyond top performance. We are opening new horizons in next-generation robotics technology through research on magnetic materials for high-performance motors, development of independent control and multi-phase control technology for motors, and establishment of optimal control systems.
01
Problems with Conventional Robot Motor Technology
Motors are the most crucial components where robots interact with humans in physical space. However, conventional servo motors for robots necessarily use high-friction reducers due to low torque density, causing excessive stiffness in robot joints. This leads to significant safety concerns, such as causing serious injuries during unexpected collisions with humans. Furthermore, the use of reducers necessitates torque sensors due to nonlinear friction, increasing the production costs of robot applications. The increased weight and size lead to inefficient operation and frequent robot damage. Therefore, future robots such as collaborative robots, humanoid robots, walking robots, wearable robots, and exoskeletons need joints that are both flexible and strong, similar to human joints.
02
Characteristics of Faraday Dynamics Motors
FaradayDynamics’ next-generation servo motors implement characteristics of human muscles. Through new magnetic material development and magnetic field concentration technology, we have achieved world-class torque density and backdrivability. With strong torque output from small current, it demonstrates optimal continuous torque and high efficiency. Additionally, it realizes precise control with less than 2% torque ripple and minimized cogging torque. This innovative technology opens new horizons in future robot development and accelerates the safe introduction of robots into human society.
03
Continuous Research and Development
FaradayDynamics pursues endless innovation beyond top performance. We are opening new horizons in next-generation robotics technology through research on magnetic materials for high-performance motors, development of independent control and multi-phase control technology for motors, and establishment of optimal control systems.
Our Process
Faraday Dynamics' Proprietary Manufacturing Facilities
FaradayDynamics manufactures over 90% of servo motor processes with in-house manufacturing facilities to provide customers with not only world-class performance quality but also cost-effectiveness. The ability to directly design and manufacture all components enables us to provide customized solutions for customer applications and produce fast and perfect custom motors.
01
Our unique solution
02
Proprietary Manufacturing Facilities
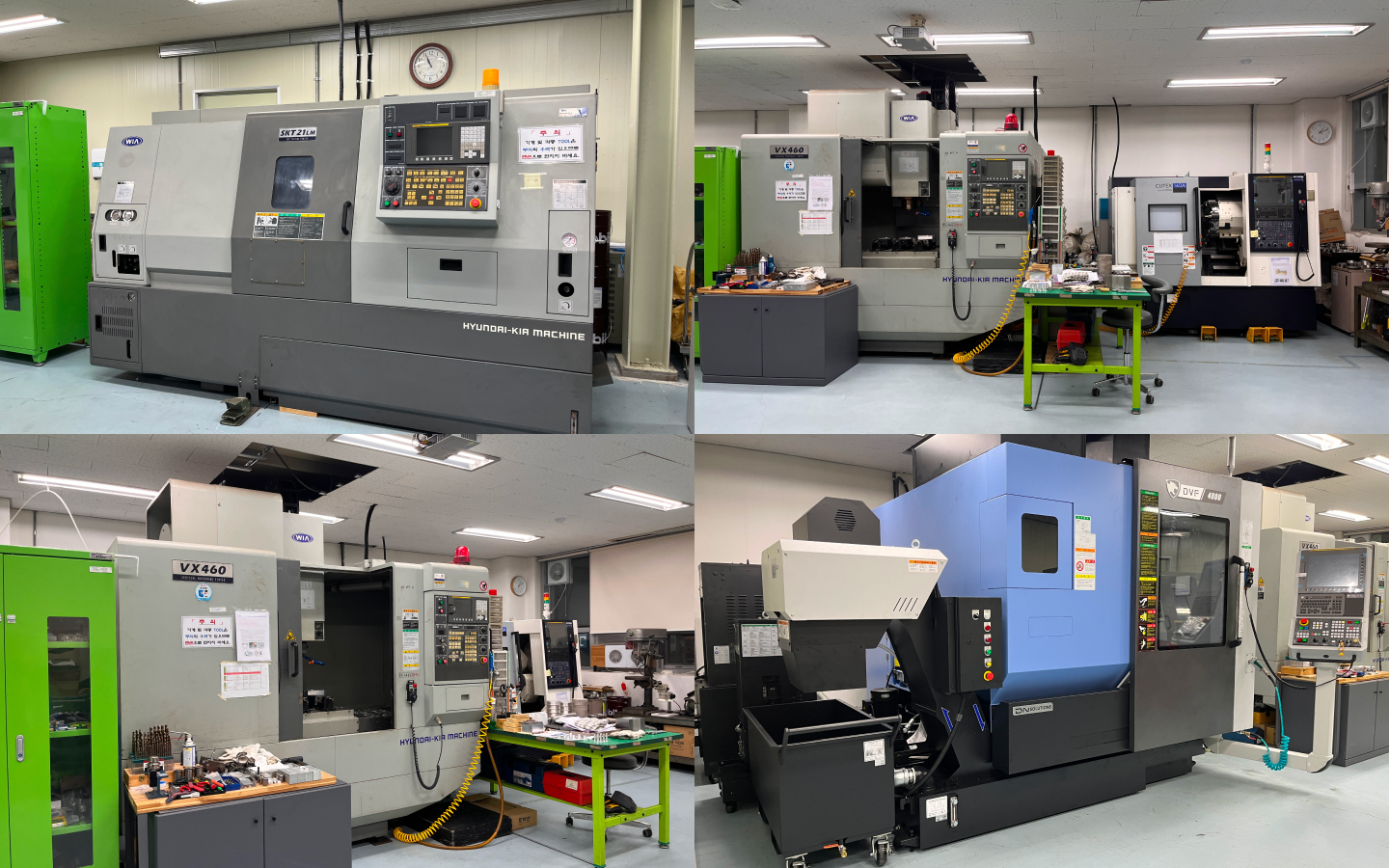
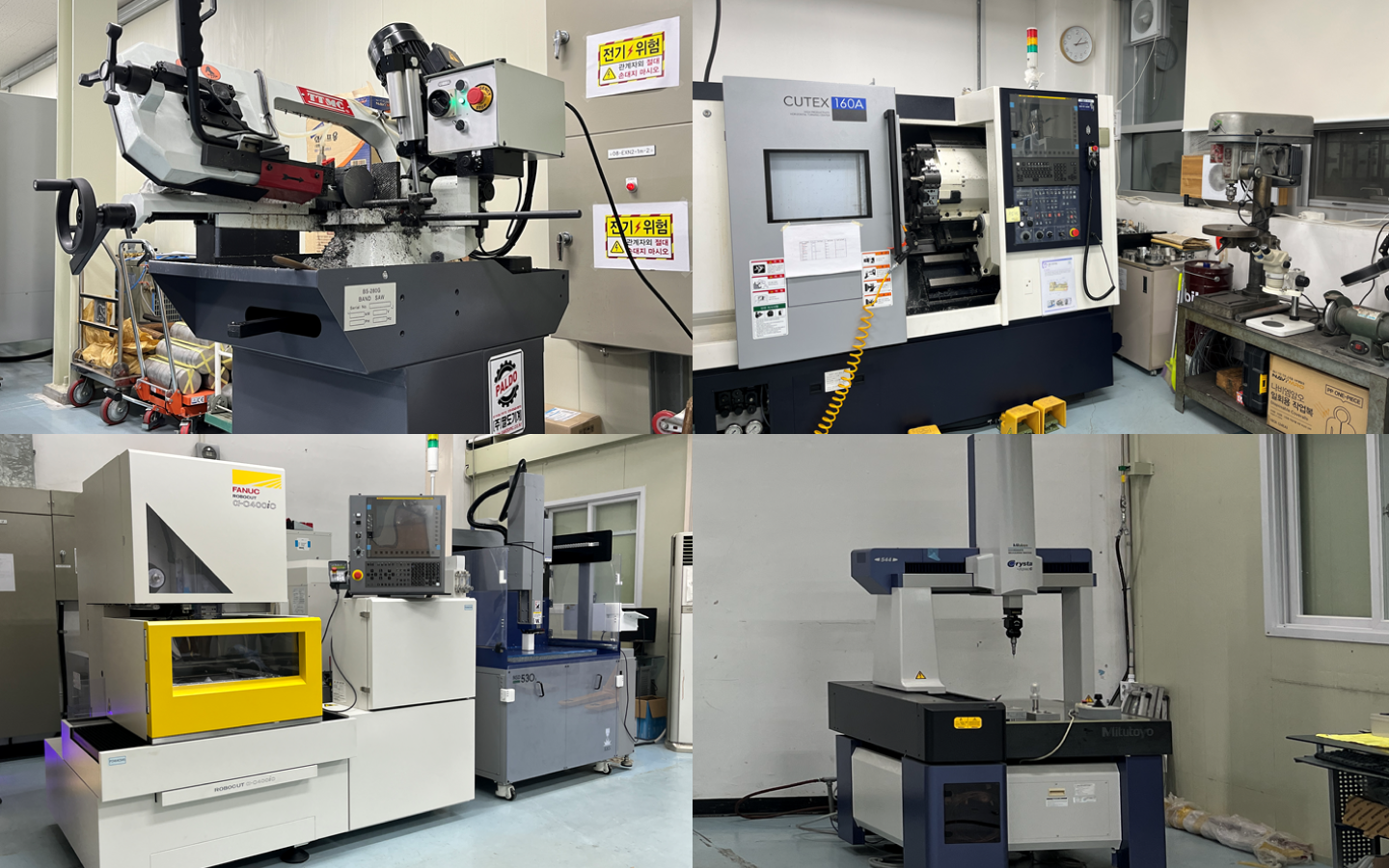
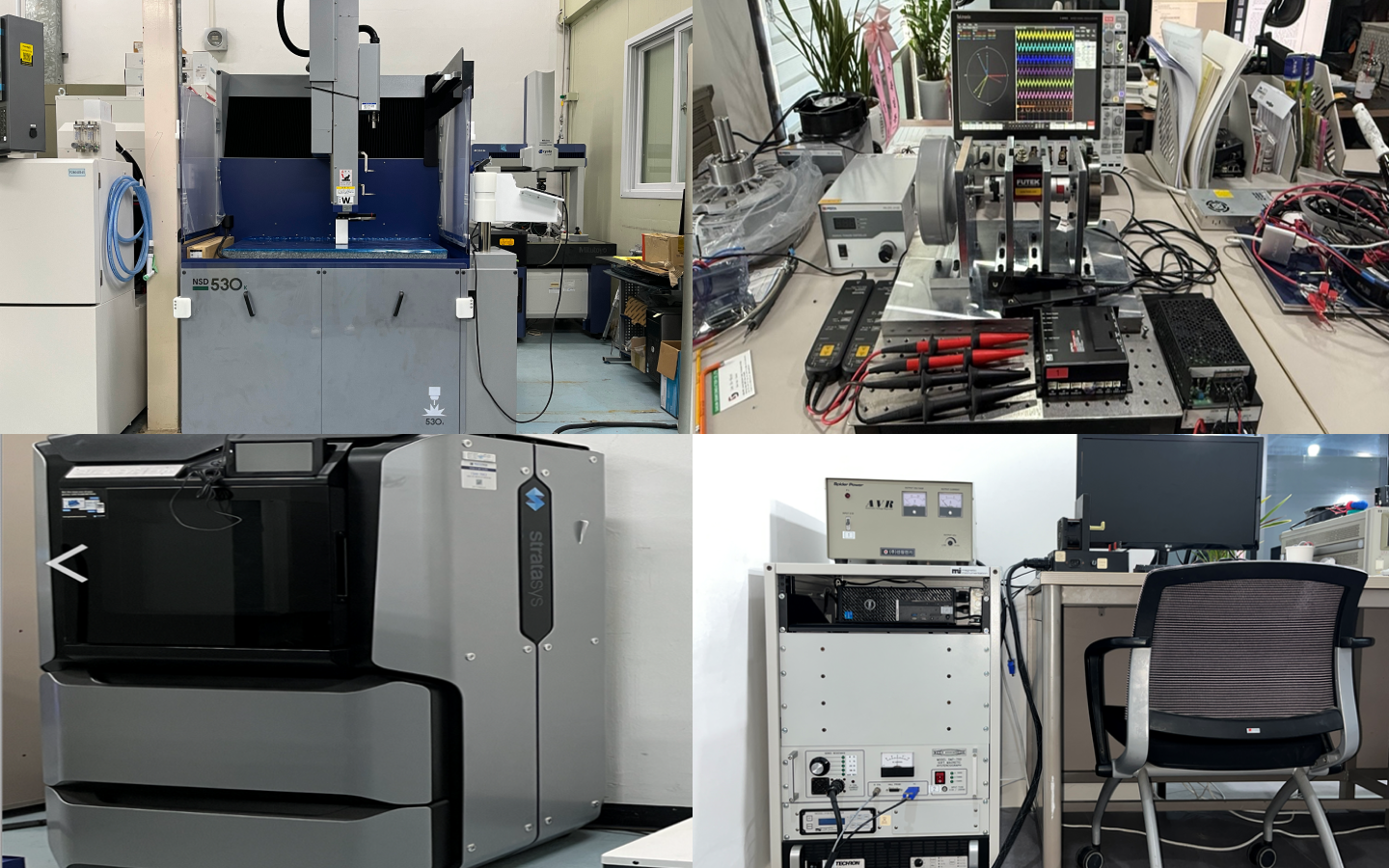
01
Our Unique Solution
02
Proprietary Manufacturing Facilities
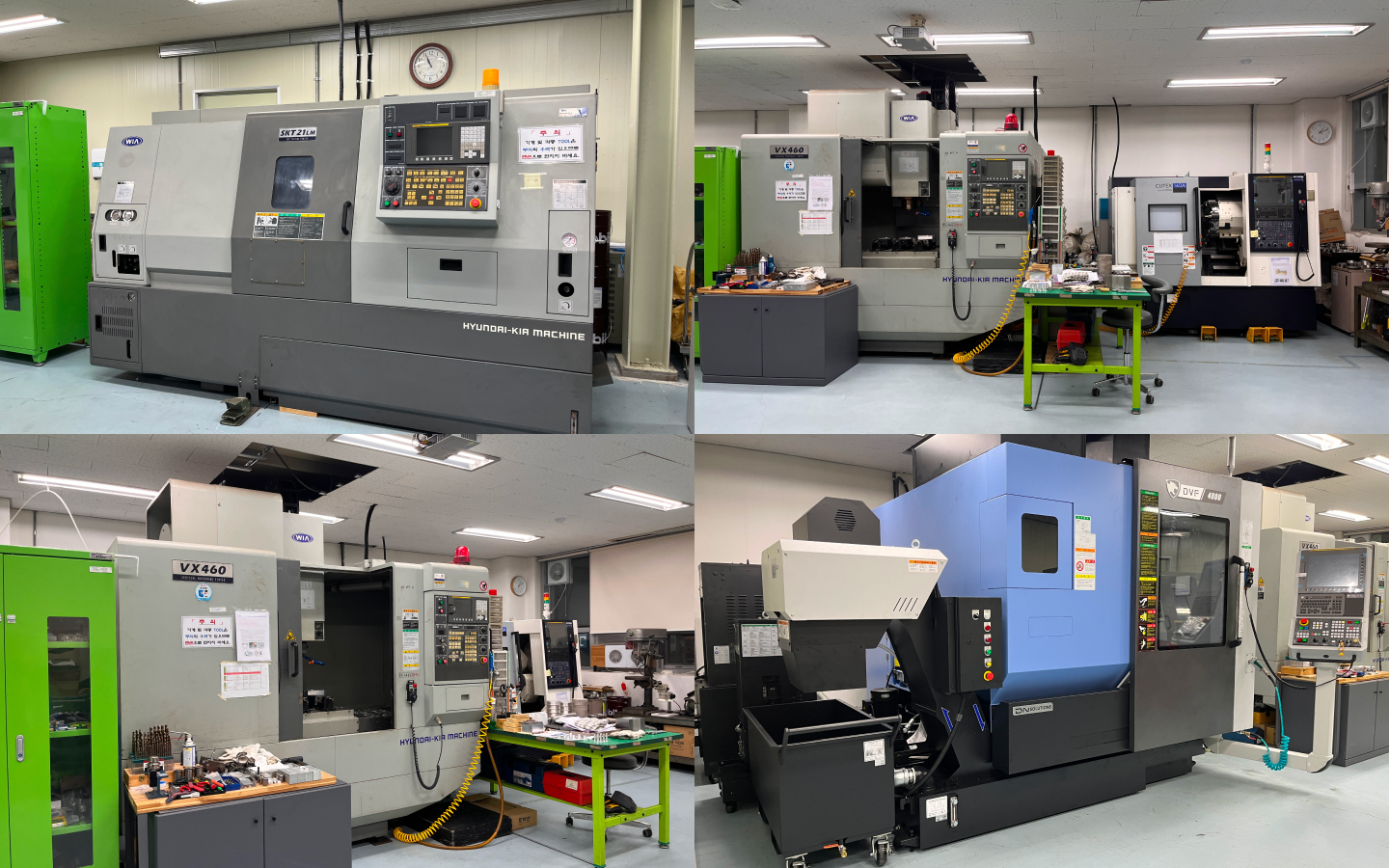
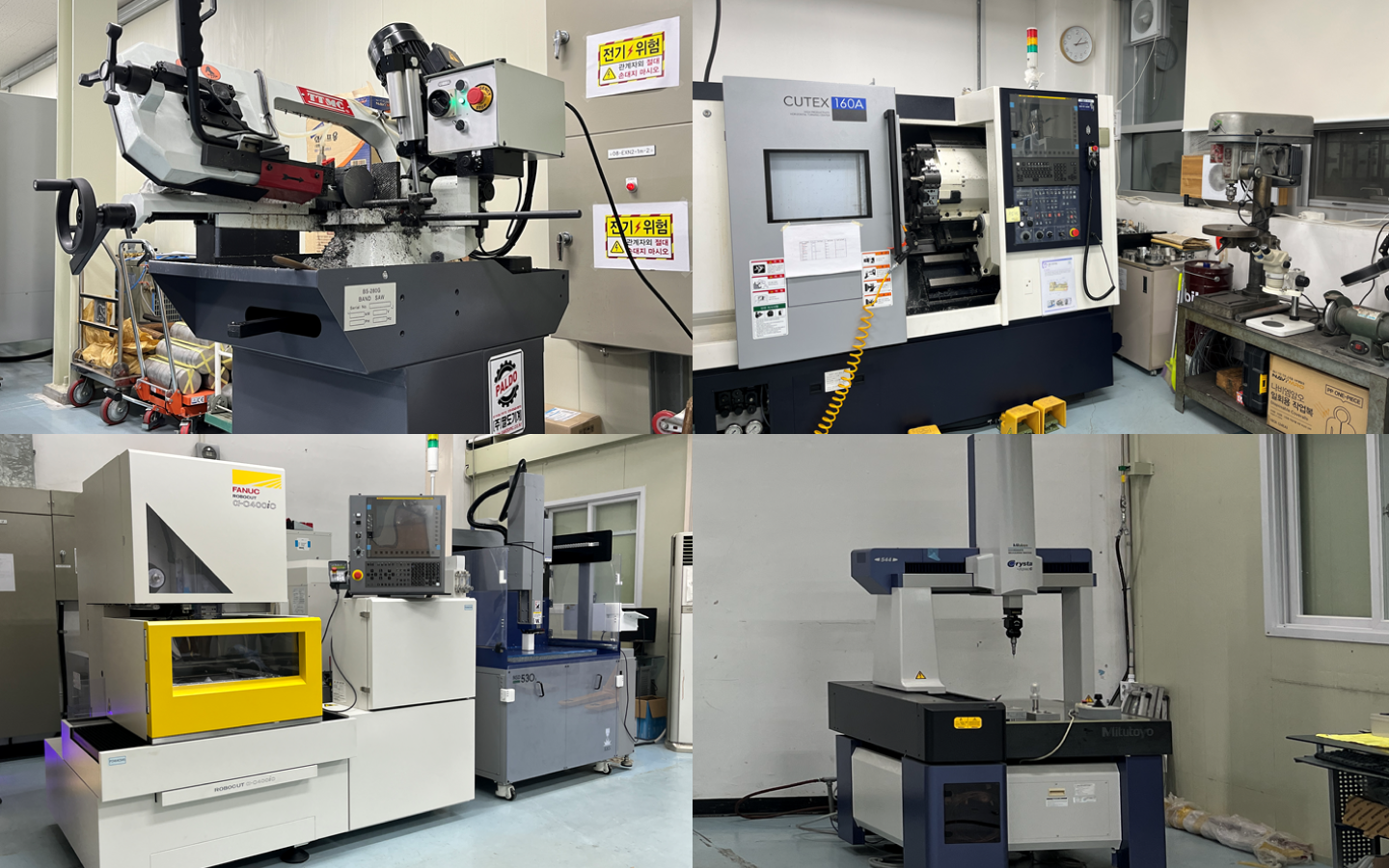
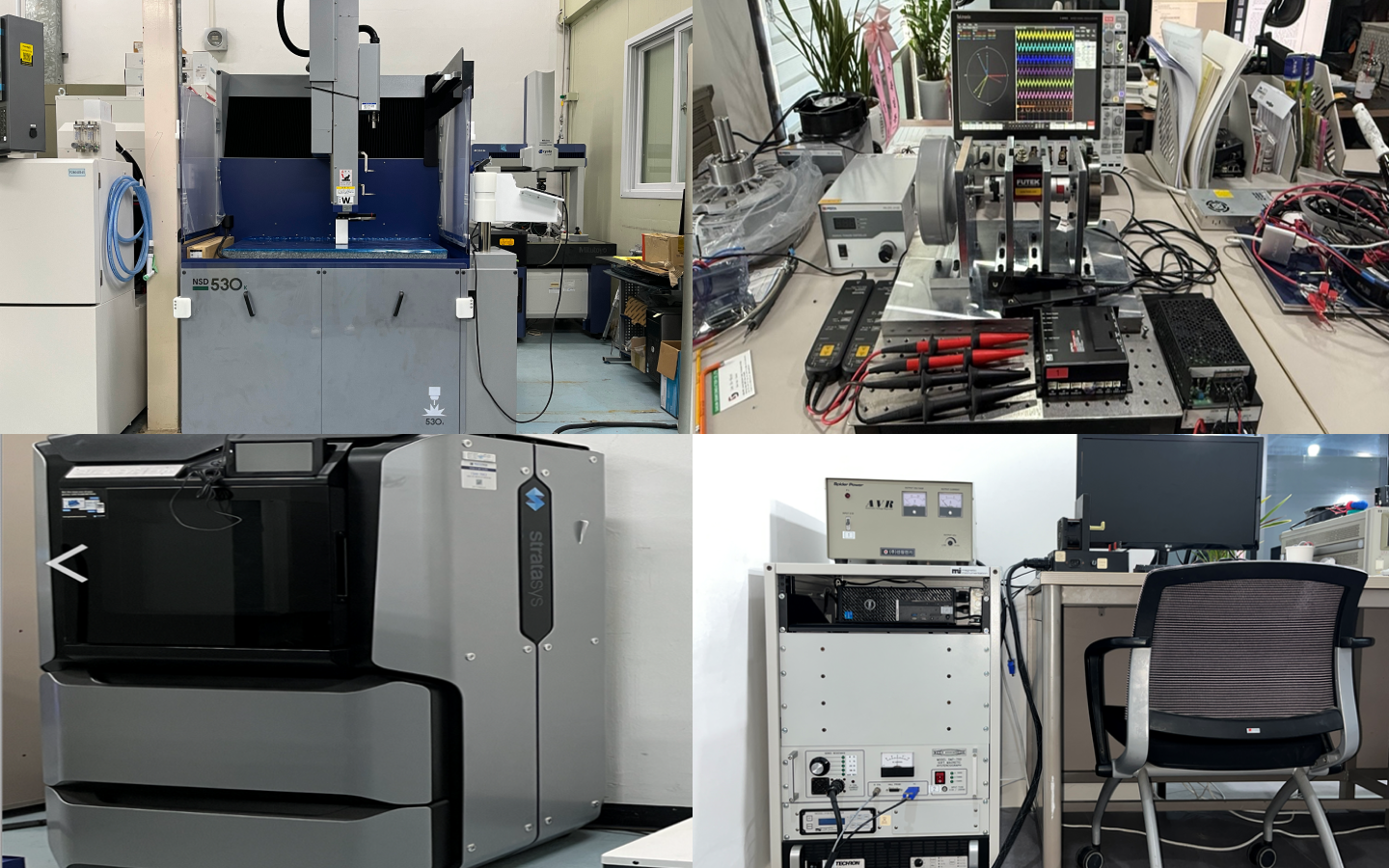